- For a large workspace of AFM, a Hybrid reluctance actuator (HRA) is desired to move its probe vertically.
- For required motion performances, a HRA for AFM is developed by integrating a Hall sensor to compensate for problematic magnetic hysteresis.
- Experiments successfully demonstrate that the hysteresis is decreased from 3.96% to 1.63%.
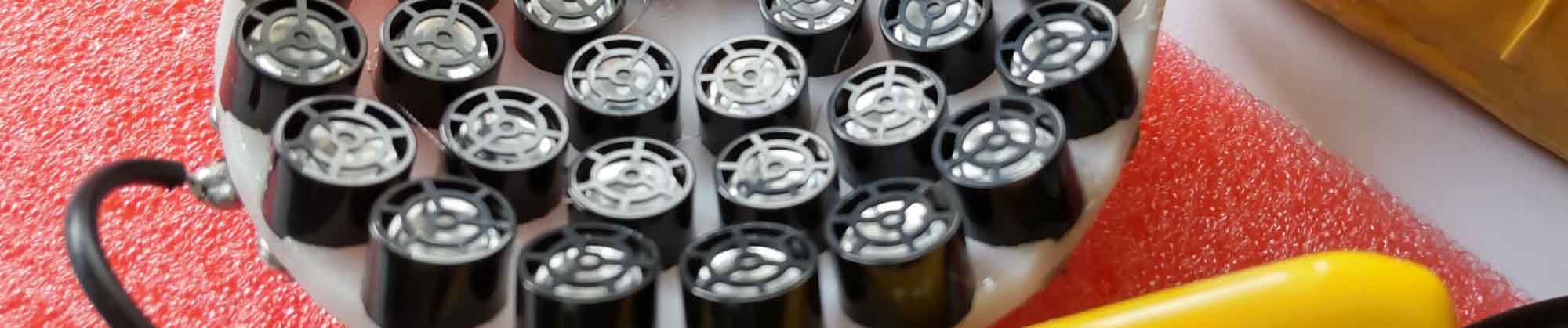
Mechatronics Laboratory
福井大学メカトロニクス研究室
Flux-controlled Hybrid Reluctance Actuator for Atomic Force Microscopy
Project Summary
Project Description
Introduction
An atomic force microscope (AFM) enables high-resolution imaging and sample manipulation by moving its probe with nanometer resolution. For the vertical motion, a piezoelectric actuator is mostly used, and its motion range is limited to approximately 10 micrometers in a tradeoff with the control bandwidth. To overcome the range-bandwidth tradeoff for a high-speed, large probe motion, development of an AFM with a hybrid reluctance actuator (HRA) as the vertical high-precision actuator is desired. HRAs realize motion with nanometer resolution and achieve a motor constant higher than comparable Lorentz actuators. However, HRAs exhibit nonlinear magnetic hysteresis, as seen in a B-H curve. To compensate for the nonlinearity, this project proposes and develops a HRA that integrates a Hall sensor and controls magnetic fluxes for the high-precision vertical probe motion of an AFM. An advantage of the proposed HRA is that the nonlinearity can be compensated at low frequencies, unlike conventional search coils.
HRA with integrated Hall sensor for AFM
Fig. 1 shows an AFM where the probe is vertically moved by a HRA. Leaf-spring flexures vertically guide a mover, to which a rod is attached to mount a probe. The stator has a permanent magnet and coils and provides magnetic fluxes to generate a reluctance force for the vertical actuation of the mover with the probe. For flux control, the magnetic fluxes are measured by a Hall sensor.
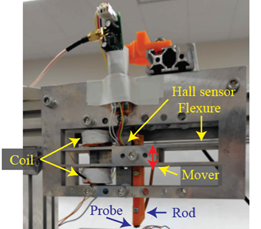
Hysteresis compensation
In conventional HRAs, coil currents are controlled by feedback control. A problem is that the resulting fluxes include hysteresis. In contrast, the proposed HRA can measure the magnetic fluxes with hysteresis by using the Hall sensor, and the nonlinearity is compensated by feedback control for precision motion.
To experimentally validate the effectiveness of the proposed HRA, PI controllers are designed individually for conventional current control and flux control. For fair comparison, they are tuned to achieve a cross-over frequency of about 2 kHz. With the designed controllers, sine references are used to generate a motion of about 10 um at 10 Hz, and it is measured by an interferometer.
Fig. 2 shows the measured results. When the conventional current controller is used, a nonlinearity of 3.96% is observed due to hysteresis in Fig. 2 (right). It is reduced to 1.63% by using the flux feedback controller in Fig. 2 (left), successfully demonstrating the effectiveness of the proposed HRA.
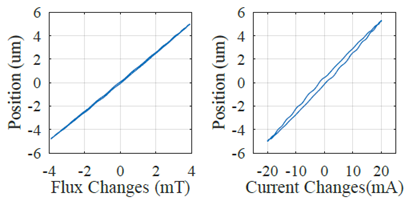
Applications
- Nanomanufacturing and nanoassembly with a large workspace
- High topography imaging
Related articles
- N. Takeuchi, K. Takahashi, T. Fukuyama, A. Yamashita, and S. Ito, "Hysteresis Compensation by Flux-Controlled Hybrid Reluctance Actuator with Integrated Hall Sensor," IEEJ international workshop on Sensing, Actuation, Motion Control, and Optimization, 2025.
- K. Takahashi, S. Ito, "Real-time Estimation of High-precision Actuator's Variable Stiffness for Vibration Isolation," IFAC Symposium on Mechatronic Systems, Accepted.
Project evaluation
This project has been evaluated by an external professional with the following comments:
- "To tackle a challenging issue of nanoscale measurement, a new approach has been taken by considering both hardware and software aspects to achieve nice results, which is excellent." Yuki Iwano, Professor, Fukui University of Technology.
Funding
This work was supported in part by JKA and its promotion funds from KEIRIN RACE.
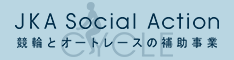
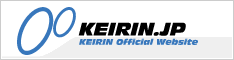