- An end-effector with a 1-DOF high-precision actuator is developed for tasks of a robot arm with nanometer resolution.
- Sample-tracking vibration isolation is implemented, where a flexure-guided mover of the high-precision actuator is tracking a sample or target by isolating vibrations.
- To efficiently isolate vibrations from the robot, the high-precision actuator’s electromagnetic stiffness cancels the flexure stiffness for quasi-zero stiffness.
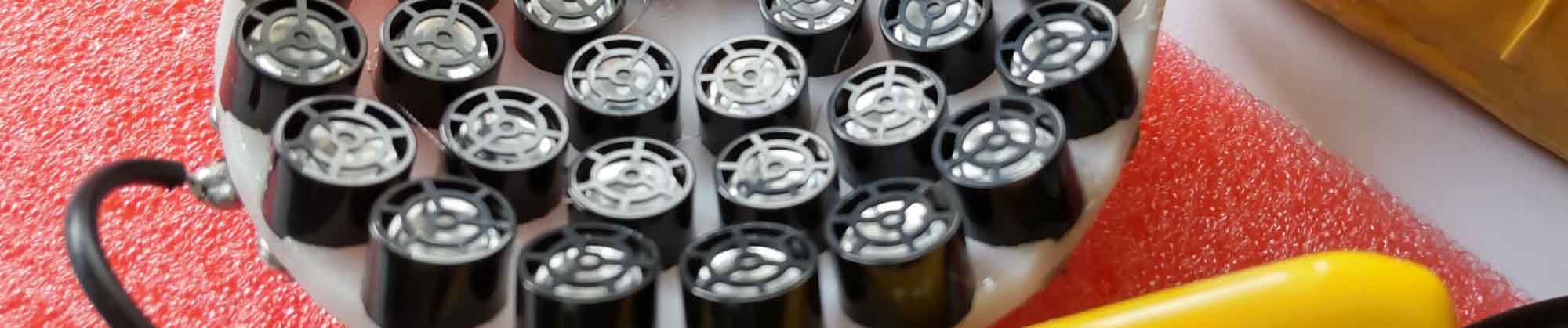
Mechatronics Laboratory
福井大学メカトロニクス研究室
Robot End-effector Integrating 1-DOF High-precision Actuator with Quasi-zero Stiffness for Nanopositioning
Project Summary
Project Description
Introduction
To manufacture, assemble, and inspect goods with nanometer resolution on a production site, industrial robots that can move with high-precision motions are desired. However, typical off-the-shelf industrial robots have a repeatability of micrometers or more, for example, due to their actuation mechanisms. Additionally, disturbances such as floor vibrations and vibrations generated by the robots themselves are problematic to carry out tasks with nanometer resolution. For highly precise robot motions by overcoming those challenges, this project develops an end-effector with a high-precision actuator to implement sample-tracking vibration isolation as a case study.
Sample-tracking vibration isolation for a robot end-effector
Fig. 1 illustrates a development concept with sample-tracking vibration isolation. To isolate and reject vibrations at the robot arm tip, the end-effector consists of a high-precision actuator to vertically position a mover and a position sensor to measure a distance to a target. The measured distance is controlled by the high-precision actuator and a feedback controller, such that the vibrations from the robot are rejected to carry out tasks highly precisely.

End-effector with quasi-zero stiffness
Although the achievable vibration performance of sample-tracking vibration isolation is improved by feedback control design to some extent, mechanical resonances of the end-effector restrict control bandwidth and performance [Ito et al., Mechatronics, 44, 2017]. To achieve higher vibration isolation performance, quasi-zero stiffness is implemented between the robot arm tip and the end-effector’s mover.
The mover is suspended by flexures to compensate for gravity with high energy efficiency, as shown in Fig. 2. However, they have a stiffness of k_f in Fig. 1, which transmits vibrations from the robot arm tip to the mover. To cancel it, a reluctance actuator is selected as the high-precision actuator. Reluctance actuators have an advantage of a force larger than a comparable Lorentz actuator, which is commonly used for nanopositioning. However, they have nonlinearities and a negative stiffness, which are typically regarded as unwanted properties. In this project, the reluctance actuator is linearized with a permanent magnet, and its negative stiffness k_a is utilized to cancel the flexure stiffness to realize quasi-zero stiffness (i.e. k_f = k_a).
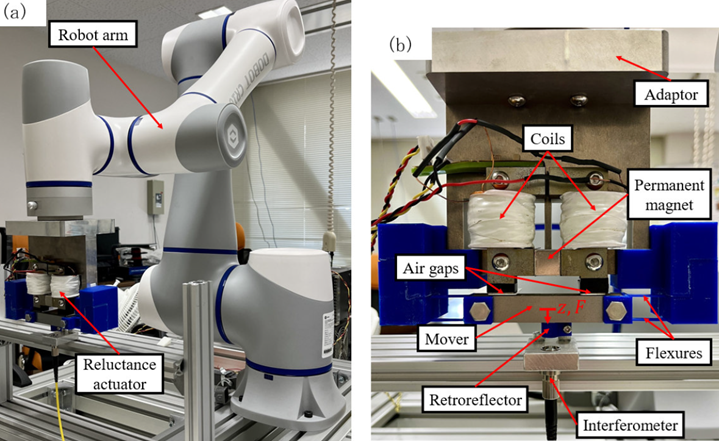
To experimentally validate the proposed end-effector, impulse-like responses are measured. An external shock is applied to the robot arm tip when the feedback control is turned on without tuning the negative stiffness, and the tracking error is measured. Experiments are repeated when the negative stiffness is fine-tuned for quasi-zero stiffness with feedback control.
The results are shown in Fig. 3. Without tuning the negative stiffness, the tracking error has a peak-to-peak value of 1522 nm. The quasi-zero stiffness successfully decreases the large error by 68 % to 491 nm. The corresponding power spectral density (PSD) in Fig. 3(bottom) reveals that the stiffness cancellation is effective between 1 Hz and 60 Hz. Particularly around 10 Hz, the PSD is decreased by 96 % by utilizing the quasi-zero stiffness. Overall, the experimental results successfully demonstrate the effectiveness of the developed end-effector for a robot to isolate vibrations from the arm tip by canceling the flexure stiffness by the negative stiffness of the high-precision reluctance actuator.
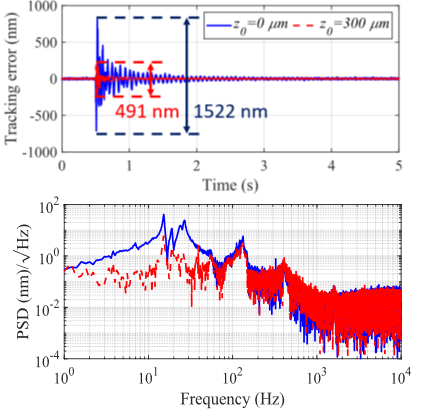
Applications
- Nanomanufacturing and nanoassembly
- High-precision robots
- Inline metrology with nanometer resolution
Related articles
- K Takahashi, R Makino, and S Ito, "Sample-tracking vibration isolation with rigid negative stiffness for broad bandwidth," Mechatronics, 99, 2024.
- T. Fukuyama, K. Takahashi, A. Yamashita, and S. Ito, "Reluctance actuator with integrated Hall sensor and permanent magnet for vibration isolation," IEEJ international workshop on Sensing, Actuation, Motion Control, and Optimization, pp. 477-480, 2024 (Best Presentation Award).
- K Takahashi, R Makino, and S Ito, "Vibration Isolator using Hybrid Reluctance Actuator toward Quasi-zero Stiffness," IFAC-PapersOnLine, 56 (2), pp. 3392-3397, 2023.
Project evaluation
This project has been evaluated by a committee with external professionals, whose comments are summarized, as follows:
- "Effects of the quasi-zero stiffness have been successfully demonstrated, and the project opens up new possibilities for precision motion systems." Naoki Motoi, Associate Professor, Kobe University
- "The research has many applications, such as laser focusing for optical systems, and we look forward to further research for practical applications." Sentoku Eisuke, Associate Professor, National Institute of Technology, Fukui College
Funding
This work was supported in part by JKA and its promotion funds from KEIRIN RACE.
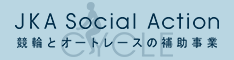
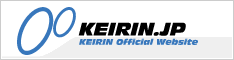